
ReMining Plastic™
ReMining Plastic™ is dedicated to converting all plastic materials into commercially viable byproducts, utilizing the plastic waste stream from recycling and manufacturing methods. ReMining Plastic™ innovative technology in plastic recycling has created a new generation of systems that have overcome previous plastic recycling challenges. Each ReMining Plastic™ facility can divert 500 tons of plastic per day from heading to local landfills; utilizing ReMining Corporation's proprietary Transmolecular™ technology, this process converts plastics into high-end, ultra-clean, ASTM qualified fuels, chemicals, and solvents.
One ReMining Plastic™ machine can handle 50 tons of waste per day, which equates to 12,000 gallons per day or 4 million gallons of liquid fuels per year (depending on the quality of feedstock and run capacity). ReMining Plastic™ machines also have low operating and maintenance costs, which leads to higher profit revenues and lower break-even points.
The growing applications of plastic in industrial and consumer markets have put pressure on local governments and communities to solve a growing global plastic problem. Every year hundreds of millions of tons of plastics are used in the United States; approximately 80% of it ends up in a landfill, 15% ends up in an incinerator, and 5% are recycled.
ReMining Plastic™ is well-positioned to attain plastic feedstock well into the future and has the flexibility to meet consumer demand by altering the type of fuels our facility produces, as well as offering multiple high-end blends.
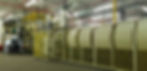
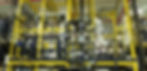

0
4,000,000
17,000
Waste discharge facility
The amount of fuel (Gal) produced by one ReMining Plastic™ machine in one year
The amount of plastic (Tons) one ReMining Plastic™ machine processes in one year

ReMining Plastic™ Products
ReMining Plastic™ byproduct benefits lie within the processing of waste plastics. ReMining Plastic™ uses a state-of-the-art Transmolecular™ technology to recapture the plastic waste stream, and produce highly-valued ASTM qualified chemicals and fuels. This extraordinary technology is vastly different from the traditional processes of dealing with the plastic waste stream (i.e., landfilling, incinerating, plastic waste in oceans, etc.) that can have a detrimental effect on ecosystems and environments.
At specific points during ReMining Plastic’s proprietary Transmolecular™ process, ReMining Plastic™ has the ability to adjust its manufacturing to develop various byproducts such as Premium Gasoline, Premium Diesel, Jet Fuel, Kerosene, various additives, and gases. This assists in maximizing our ability to manufacture highly-valued ASTM qualified fuels, chemicals, and solvents.
Q-CET™
-
Cetane Number (CN) of diesel fuel is a measure of its‘ ignition quality.' Premium to high Cetane Number diesel fuels present improved engine performance and emission reduction advantages.
-
Cetane Number booster from standard pipeline fuels.
-
Hydrocarbon boiling point range from 560° to 650° F.
-
High BTU content.
-
Shortened ignition delay. Improved diesel fuel ignition quality.
-
Improved cold start. Better fuel combustion. Better fuel economy.
-
Q-CET™ is a blend of 2-Ethylhexyl Nitrate (2-EHN) which improves the Cetane Number.
-
A blend of this product with a 40 CN #2 diesel at a 1:3 ratio will improve the fuel to premium diesel standard (~55CN) with a 25% volume addition to the entire bulk volume.
-
Low Sulfur—Less than 8ppm.
-
The hydrocarbon boiling point range is 100°–330° F (or as the customer requires).
-
Large percentages of PURE (i.e. n-octane) compounds within this"cut."
-
Extremely low Olefin content.
-
Very HIGH Napthene content.
-
Based upon the custom.
Q-SOL™
Q-KSOL™
-
Low Sulfur—Less than 8ppm.
-
Extremely LOW Olefin content.
-
Burns very “clean” with no visible smoke.
-
Hydrocarbon boiling point range is 330°–560° F (or as customer requires).
-
From winter blends to D-1, this product makes an ideal diesel fuel additive during winter months.
-
Great “feeder” product for the solvent and fuel oil industries.
-
Based upon the customers requirements, aromatic content can range from <1% to 15%.